Integration der additiven Fertigung mit der maschinellen Bearbeitung für komplexe Bauteile
Der Kern der additiven Fertigung liegt im schichtweisen Aufbau, der das Potenzial zur Herstellung hochkomplexer und maßgeschneiderter Bauteile eröffnet. Für Branchen wie die Luft- und Raumfahrt und die Medizintechnik, in denen Gewichtsreduzierung und kundenspezifische Geometrien von entscheidender Bedeutung sind, bietet die additive Fertigung eine unvergleichliche Designflexibilität.
Die additive Fertigung hatte bisher Schwierigkeiten, feine Oberflächenstrukturen oder hochpräzise Merkmale zu erreichen, die für bestimmte Anwendungen erforderlich sind. Hier kommt der hybride Ansatz ins Spiel: Durch die Integration der Bearbeitung in den Prozess können Hersteller komplexe innere Strukturen im 3D-Druck herstellen, während sie Verfahren der Laserbearbeitung oder CNC-Techniken einsetzen, um die erforderlichen Endtoleranzen und Oberflächenqualitäten für funktionale Bauteile zu erreichen.
Ein Beispiel hierfür ist ein Bauteil mit komplexen inneren Kanälen oder Untercuts, das mit einer Metallpulverbett-Schmelztechnik gedruckt werden kann. Anschließend verfeinert ein Bearbeitungsschritt die äußeren Abmessungen und sorgt für die erforderliche Präzision. Diese Methode ermöglicht es Herstellern, die Einschränkungen jeder Technik zu umgehen und bietet eine robustere Lösung für die Produktion komplexer Bauteile. Die Integration von additiver Fertigung und Zerspanung ist auch entscheidend für das 3D-Laserschneiden, bei denen Komponenten mit filigranen Geometrien gedruckt und dann mit hochpräzisem Schneiden verfeinert werden.
Warum Hybridfertigung mit Laserbearbeitung funktioniert
Die hybride Fertigung ist mehr als nur die Kombination zweier Verfahren - sie nutzt die einzigartigen Vorteile additiver und subtraktiver Verfahren zur Effizienzsteigerung.
Einer der Hauptvorteile ist die Reduzierung von Materialabfällen. Bei der traditionellen Zerspanung beginnt der Prozess mit einem festen Materialblock, und alles, was abgetragen wird, wird zu Abfall. Im Gegensatz dazu wird bei der additiven Fertigung nur dort Material hinzugefügt, wo es benötigt wird, was zu einer erheblichen Abfallverringerung führt. Wenn die beiden Verfahren kombiniert werden, schafft die additive Fertigung die komplexe Grundlage des Bauteils, während die maschinelle Bearbeitung die Feinabstimmung der Abmessungen vornimmt und so sowohl Materialeffizienz als auch Präzision gewährleistet.
Ein weiterer entscheidender Vorteil ist die Designflexibilität. Die additive Fertigung ermöglicht die Herstellung von Bauteilen, deren Bearbeitung mit herkömmlichen Methoden allein unmöglich oder teuer wäre. Komplexe Gitterstrukturen, innere Strukturen und Untercuts können direkt in das Bauteil integriert werden. Diese Freiheit im Design erleichtert auch die Herstellung von Leichtbauteilen, ein entscheidender Faktor in Branchen wie der Automobil- und Luftfahrtindustrie. Mithilfe von Laserbearbeitung können Hersteller sicherstellen, dass selbst diese komplexen Bauteile die höchsten Anforderungen an Präzision und Haltbarkeit erfüllen.
Kürzere Produktionszeiten sind ein weiterer großer Vorteil der Hybridfertigung. Hybride Systeme rationalisieren den Arbeitsablauf, indem sie die Anzahl der einzelnen Produktionsschritte minimieren, z. B. den Transfer eines Teils zwischen einem 3D-Drucker und einer CNC-Fräse. Was normalerweise mehrere Rüstvorgänge und Transfers erfordert, kann nun mit einem einzigen integrierten System durchgeführt werden, was die Vorlaufzeiten verkürzt und den Weg vom Prototyp zur Produktion beschleunigt.
The Boeing Company nutzte beispielsweise die additive Fertigung, um die Produktionszeit für Komponenten des 787 Dreamliner erheblich zu verkürzen. Durch die Einführung des 3D-Drucks für Kabinenteile wie Halterungen und Lüftungsrohre konnte Boeing die Vorlaufzeit für diese Komponenten von mehreren Wochen auf nur wenige Tage verkürzen. Dadurch wurde nicht nur der Fertigungsprozess rationalisiert, sondern auch die Material- und Arbeitskosten gesenkt.
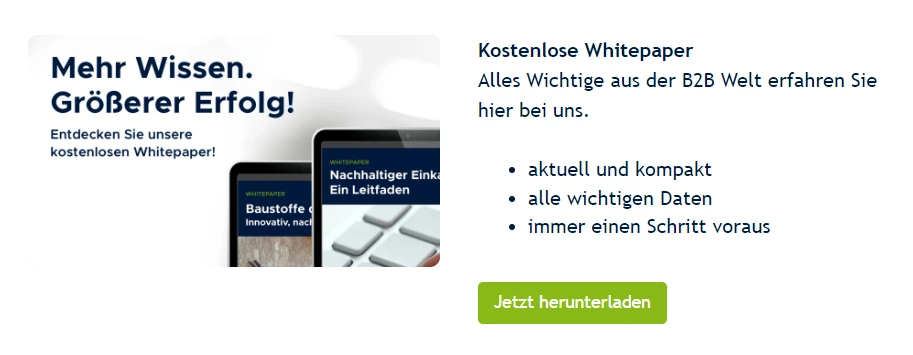
Herausforderungen und zukünftige Trends in der Hybridfertigung und Laserbearbeitung
Die Hybridfertigung bietet zwar erhebliche Vorteile, ist aber auch mit Herausforderungen verbunden. Eine der größten Hürden ist die Integration der beiden Verfahren im Bereich Zerspanung und Umformung. Um einen reibungslosen Übergang zwischen additiven und maschinellen Verfahren zu gewährleisten, sind eine präzise Kalibrierung und fortschrittliche Software erforderlich, die die Komplexität beider Arbeitsabläufe bewältigen kann.
Das Hybridsystem muss auch die Materialeigenschaften berücksichtigen, die sich während des Fertigungsprozesses ändern, insbesondere bei der Bearbeitung von Metallen. So kann beispielsweise die Wärme, die in der additiven Phase bei der Laserbearbeitung erzeugt wird, die Mikrostruktur des Materials verändern, wodurch dessen Bearbeitung erschwert wird. Folglich müssen die Hersteller die Wärmebehandlung und die Nachbearbeitungsschritte sorgfältig steuern, um die gewünschten Materialeigenschaften zu erreichen.
Eine weitere Herausforderung sind die hohen Kosten für hybride Fertigungsanlagen. Diese Systeme können zwar die Produktionseffizienz erheblich verbessern, doch die Anfangsinvestitionen sind beträchtlich, so dass sie sich eher für Branchen eignen, die mit hochwertigen Bauteilen arbeiten, wie die Luft- und Raumfahrtindustrie oder die Herstellung medizinischer Geräte. Für kleinere Hersteller können die hohen Anfangskosten ein Hindernis für die Einführung sein. Mit dem Fortschritt der Technologie und ihrer zunehmenden Verbreitung wird jedoch erwartet, dass die Kosten sinken, wodurch hybride Systeme für eine breitere Palette von Industrien zugänglicher werden.
Einer der vielversprechendsten Trends in der Hybridfertigung ist die Entwicklung automatisierter Systeme, die die Produktion weiter rationalisieren können. Fortschritte in der Laserbearbeitung und der Robotik ermöglichen bereits die Schaffung völlig autonomer Fertigungszellen, in denen Bauteile mit minimalem menschlichem Eingriff hergestellt werden. Eine weitere interessante Entwicklung ist der Einsatz der Hybridfertigung für Reparaturanwendungen. Anstatt verschlissene oder beschädigte Teile zu entsorgen, können Hersteller sie durch das 3D-Laserschneiden und additiven Verfahren wiederherstellen und so ihre Lebensdauer verlängern und den Abfall reduzieren.
Neue Möglichkeiten in der Hybridfertigung und Laserbearbeitung erschließen
Die Integration von additiver Fertigung und maschineller Bearbeitung bietet Herstellern, die ihre Produktionskapazitäten im Bereich Zerspanung und Umformung verbessern wollen, einen spannenden Weg in die Zukunft. Mit der weiteren Entwicklung dieser Hybridsysteme werden weitere Verkürzungen der Durchlaufzeiten, eine höhere Materialeffizienz und eine Ausweitung ihrer Anwendungen in verschiedenen Branchen erwartet.
In der Zukunft könnte die Digitalisierung von Fertigungsabläufen eine neue Dimension erreichen, indem künstliche Intelligenz (KI) zur Simulation eingesetzt wird. Diese Simulationssoftware wird dabei in der Lage sein, die optimale Kombination aus additiven und subtraktiven Verfahren für ein bestimmtes Bauteil vorherzusagen. Beispielsweise werden prädiktive KI-Algorithmen bereits im medizinischen Bereich eingesetzt, um potenzielle Impfstoffformeln mit der höchsten Effizienz zu finden. Dies könnte die Produktion weiter optimieren, Kosten senken und die Leistungsfähigkeit von Bauteilen verbessern sowie neue Möglichkeiten für Hersteller weltweit eröffnen.